The TRB’s internal design gives it the ability to support radial and thrust loads simultaneously.
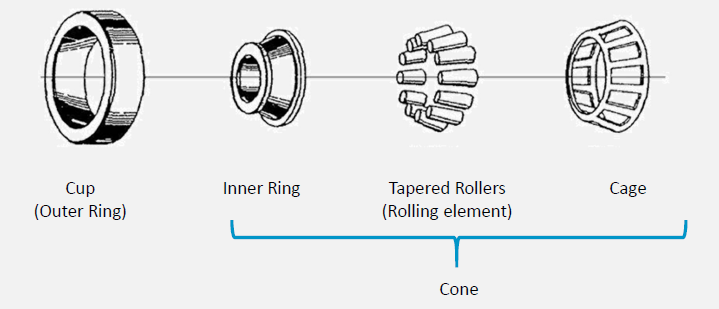
Types of Tapered Roller Bearings
- Single Row
- Double Row
- Single Row Bearings with spacers
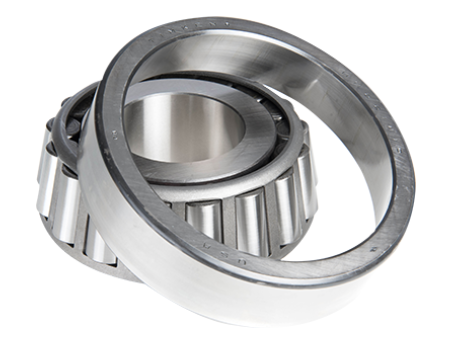
Single row
- Single row Tapered Roller Bearing (TRB) are the most common configuration
- Consists of two main separable parts: Cone assembly (inner ring, cage and rollers) and cup (outer ring)
- Typically mounted in opposing pairs on a shaft
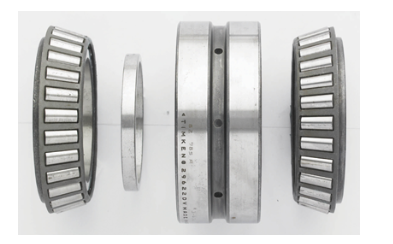
Double Row
- Feature double cup and two singles cones
- Most commonly sold with cone spacer to control the axial internal clearance to eliminate the adjustment procedure
- The bearing cone, cup and spacers are sold as a matched bearing assembly (MBA), so components cannot be mixed with other components from another bearing assembly
- Bench end play (BEP), or clearance before the bearing is installed, is marked on the spacer to make it easy for customer to identify and reorder
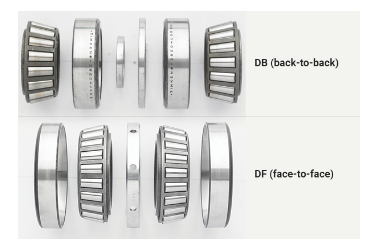
Single Row Bearings with spacers
- TS bearing are mount either in a DB (back-to-back) arrangement or DF (front-to-front) configuration
- In either case, 1 or 2 spacers control the axial internal clearance to eliminate the adjustment procedure
- The bearing cone, cup and spacers are sold as matched bearing assembly (MBA) so components cannot be mixed
- Bench end play (BEP) is marked on the spacer to make it easy for customer to identify and reorder.
Part Numbering Systems
TRBs have multiple part numbering systems falling under the ABMA or ISO standards. Let’s review the ABMA inch system and original ISO metric system.
ORIGINAL ISO PART-NUMBERING
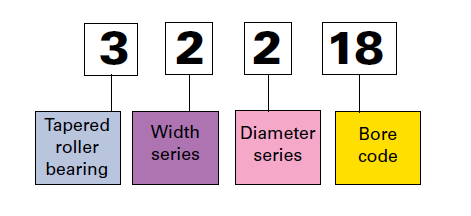
The original metric part-numbering system for tapered roller bearing was based on the ISO 15 dimensional plan for radial bearing.
ISO 355 PART NUMBERING
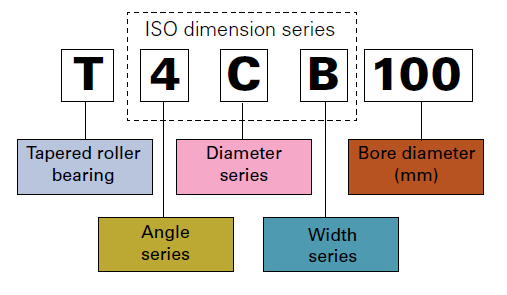
ISO introduce a new numbering system for tapered roller bearing in the ISO 355 plan. This numbering system uses three alphanumeric fields to define a dimension series. The bearing part number is defined by adding the inner ring bore diameter after the dimension series.
J-LINE PART NUMBERS
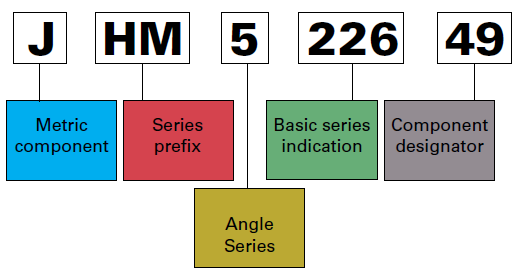
ABMA (inch) part number designed with metric envelop dimension are identified with a J-prefix. Many of these part numbers have been assigned an ISO dimension series.
J-PREFIX
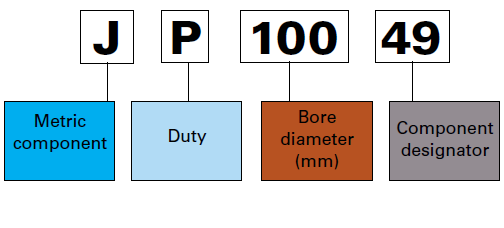
The latest ISO 355 plan includes an expanded range of metric bearings originally designed by the Timken Company. These bearings are identified with a J-prefix.
Reliability:
Expert craftsmanship, well-equipped production facilities and an ongoing investment in technology ensure our products are synonymous with quality and reliability. Our tapered roller bearings stand up to extreme situations, including high-corrosive, high-temperature, vacuum or low-lubrication environments.
Versatility:
Use Timken tapered roller bearings to help your equipment excel when it faces combined radial and thrust loads. Our bearings are uniquely designed to manage both types of loads on rotating shafts and in housings.
Design Feature:
Each tapered roller bearing contains four interdependent components the cone (inner ring), the cup (outer ring), tapered rollers (rolling elements) and the cage (roller retainer).
Mounting:
Tapered roller bearings are designed to take both radial and thrust loading. Under radial loads, a force is generated in the axial direction that must be counteracted. As a result, tapered roller bearings are normally adjusted against a second bearing. They can be mounted in either a direct or indirect mounting arrangement shown in fig.
Features | Advantages | Benefits |
Line (full) contact | ◾ Reduced contact stress between races and rollers ◾ High static load carrying ability ◾ High dynamic load carrying ability | ◾ Longer bearing life ◾ Reduced maintenance ◾ Smaller tapered roller bearing carries greater loads |
Combined load capability | ◾ Appropriate for combined load applications where other bearing type could not be used ◾ Improved reliability. ◾ Smaller tapered bearing can handle same total load as larger bearings of other design | ◾ Longer bearing life in applications with combined loads ◾ Most economical solution in applications with combined loads |
Positive roller alignment | ◾ Reduced torque ◾ Constant, true rolling motion ◾ Avoids skewing | ◾ Reduced energy costs to run equipment ◾ Reduced bearing wear, providing longer life ◾ Less maintenance and repair |
Adjustable setting | ◾ Bearings with endplay compensate for expansion on warm-up ◾ Properly adjusted bearings have less torque ◾ Bearings run quieter | ◾ Can be adjusted to fit customer’s exact needs ◾ Precise alignment for high precision, like machine tools and printing presses ◾ Longer bearing life ◾ Reduced maintenance and repair costs ◾ Less energy required ◾ Reduced noise levels |
True Rolling motion | ◾ Reduced torque ◾ Reduced heat ◾ Reduced wear | ◾ Reduced energy costs to run equipment ◾Reduced bearing wear, providing longer life ◾Less maintenance and repair. |
Good Lubrication | ◾ Better lubrication in critical large rib end area ◾ Even lubrication across the body of the rollers ◾Reduced torque ◾ Reduced heat and friction | ◾ Reduced energy costs to run equipment ◾ Reduced bearing wear ◾ Longer bearing life ◾Less maintenance and repair. |
Case carburization | ◾Hard exterior and raceways reduce wear and resist damage ◾ Resilient inner core absorbs shock loads without cracking | ◾ Longer bearing life ◾ Reduced maintenance ◾ Reduced possibility of catastrophic damage |
Note: For more details of part numbering system refer the link
Note: Search for a bearing and then navigate to Tolerances, Periodic Frequencies, Bearing Life or Part Details refer the link